One-Stop Die Casting Services for Your Projects
Need high-quality die-cast parts quickly and cost-effectively? With surface finishing or additional post-processing? At FACTUREE, we provide everything you need from a single source, tailored to your specific requirements.
The die casting process is ideally suited for components in industries such as automotive, electronics, consumer goods, medical technology, and aerospace. It enables the cost-efficient production of complex geometries with outstanding strength and excellent surface quality.
Rely on die casting for your demanding projects and benefit from the material variety, quality, and efficiency of our extensive manufacturing network – coupled with the relief we provide in supplier search and personalized consultation.
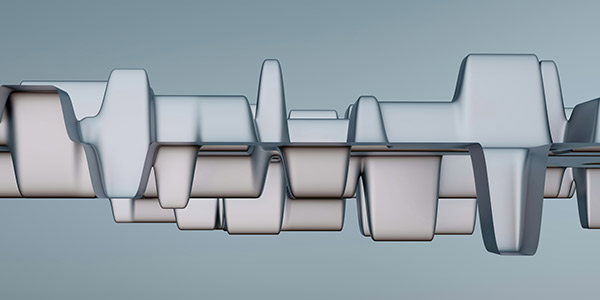
Advantages of Die Casting with FACTUREE
For the mass production of complex metal parts, the die casting process is considered the preferred manufacturing method. In this process, molten metal is pressed into permanent molds made of stainless steel under high pressure. The versatility of die casting is characterized by a wide range of available materials. The most common materials are aluminum, zinc, and magnesium alloys.
Whether you need high-strength and lightweight components for aerospace, robust and durable parts for the automotive industry, or precise and complex components for electronics – FACTUREE is your reliable partner for your demanding die casting projects.
We combine high precision, fast delivery times, and comprehensive flexibility. With our extensive network of manufacturing partners, we offer customized solutions for complex geometries and demanding applications, where quality and cost-effectiveness are equally prioritized.
Our Services at a Glance:
- Aluminum, zinc, and magnesium alloys
- Hot chamber and cold chamber die casting processes
- Ideal for mass production
- Suitable for quantities starting from 1000 pieces
- ISO 9001:2015 certified
- Industry-standard DFM
- Sampling before mass production
Different Types of Die Casting Processes
With FACTUREE, you can bring your ideas to life and develop your products with ease. Die casting offers numerous material options, each with different properties and advantages.
Each material has specific characteristics that make it particularly suitable for certain applications. In addition to aluminum die casting, we also offer zinc and magnesium die casting.
Material Options for Your Die Cast Components
Choosing the right material depends on the requirements of the final product, such as strength, flexibility, heat resistance, and chemical resistance.
Aluminum die casting combines lightness, strength, and corrosion resistance, making it a preferred solution for various industrial applications.
- High corrosion resistance
- Good thermal conductivity
- Excellent strength-to-weight ratio
- Ideal for applications where low weight is crucial
- High production speed – making it particularly suitable for mass production
- Highly demanded in the automotive, electronics, and consumer goods industries
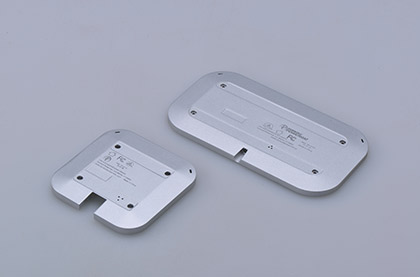
- Excellent formability and strength
- Widely used in hardware, electronics, and toy manufacturing
- Widely used in hardware, electronics, and toy manufacturing
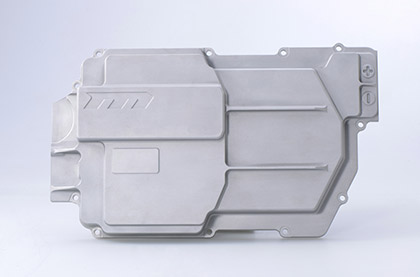
- Extremely lightweight and strong
- Excellent damping properties
- Used in the automotive and electronics industries

Finishing Options and Post-Processing of Die Cast Parts
Your die cast parts can be refined through various processes. The surfaces are treated to meet different requirements, which can be both decorative and functional. We offer a variety of surface treatment processes, such as:
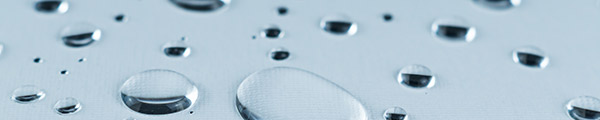
- Blasting
- Grinding
- Polishing
- Engraving
- Degreasing
- Pickling
- Etching
- Chromating
- Phosphate conversion coating
- Electroless nickel plating
- Copper plating
- Nickel plating
- Chrome plating (mainly for zinc)
- Anodizing (mainly for aluminum)
- Varnishing
- Powder coating
- Cataphoretic dip coating (KTL)
And We offer more: Additional Processes
for Metal and Plastic Parts Manufacturing
Besides die casting, we have other processes in our portfolio, each with specific advantages for different application areas – from batch size 1 to mass production:
Ideal for mass production. Suitable for complex parts with precise details and tight tolerances. Proven for various applications in industries such as automotive, electronics, medical technology, packaging, and consumer goods.
Particularly suitable for the production of highly precise components with smooth surfaces and fine details. The process is ideal for producing prototypes, small series, and decorative parts in various industries such as automotive, aerospace, and electronics.
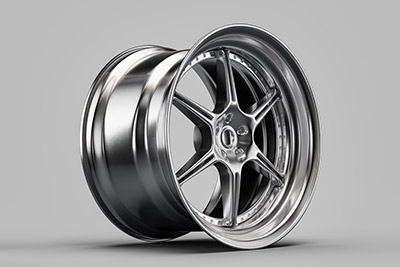
Gravity Casting
Particularly suitable for the production of components with large dimensions and a high material density. This process is often used for the production of cast parts with uniform density and low porosity, as required in the aerospace and mechanical engineering industries.