Shape the Future – with Our Injection Molding Services
Do you need plastic parts in series production? For example, complex parts with precise details and tight tolerances? Injection molding is ideal for this and much more.
It is proven for numerous applications in industries such as automotive, electronics, medical technology, packaging, and consumer goods. At FACTUREE, you get your parts quickly, cost-efficiently, and in high quality, optionally with surface finishing or further post-processing. With personal consultation for your individual requirements.
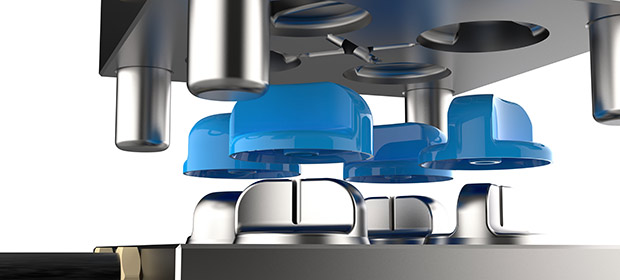
Advantages of Injection Molding at FACTUREE
We offer the right solutions for your project. We can fulfill your desires and needs in the best and most efficient way possible:
-
Cost Efficiency
Production of large quantities with low production costs -
Versatility
Efficient processing of a wide range of plastic materials
-
Precision
Even with complex geometries (tight tolerances/accurate dimensions) -
Everything from a single source
ncluding all common post-processings such as surface finishing, engravings, etc. -
Customization and Flexibility
All requirements can be implemented – tailor-made -
Personal Contact
Competent and personal consultation by experts
Different Types of Injection Molding Processes
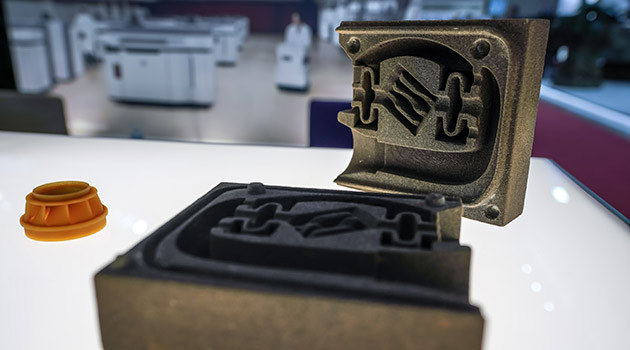
With us, you can turn your ideas into reality and develop your products with ease. We offer you:
- Conventional Injection Molding
-
Insert Molding
- Over Molding
- Rapid Injection Molding
- From DFM through mold making and sampling to series production: Everything from a single source
Dimensions and Tolerances
In the injection molding process, precise dimensions and tight tolerances are crucial as they ensure the fit and functionality of the manufactured parts. Only if the dimensions are adhered to precisely can the parts be correctly assembled and function reliably. In safety-critical industries such as automotive or medical, exact tolerances also ensure compliance with strict safety standards. In safety-critical industries such as automotive or medical, exact tolerances also ensure compliance with strict safety standards.
FACTUREE enables the precise production of components in the injection molding process – with a wide range of dimensions and the best possible tolerances. The advanced manufacturing methods and state-of-the-art machines in our large manufacturing network ensure the reliable implementation of your specific requirements for shape, size, and precision.
Material Options for Your Injection Molded Parts
Our material options offer a wide range of mechanical, thermal, and chemical properties to meet the requirements of various applications. FACTUREE supplies your injection molded parts in all materials common to the process.
In addition to widely used injection molding materials such as polypropylene (PP), ABS, polyethylene (PE), and polystyrene (PS), our range includes more than 30 other material options. Your personal contact will be happy to help you find the right material for your project.
- Acrylonitrile Butadiene Styrene (ABS)
- Polystyrene (PS)
- Polypropylene (PP)
- Polyethylene (PE)
- Polyamides (PA)
- Polymethyl methacrylate (PMMA)
- Polycarbonates (PC)
- Polyoxymethylene (POM)
- and others
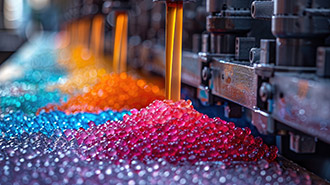
- TPE
- and others
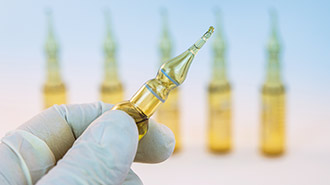
- Polytetrafluoroethylene (PTFE)
- Silicone rubber
- Resins
- and others

- Polyetheretherketone (PEEK)
- Polyetherimides (PEI)
- Liquid Crystal Polymers (LCP)
- Polyphenylene sulfide (PPS)
- Polysulfone (PSU)
- and others
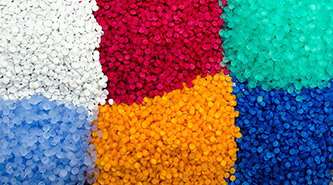
Refinement Options for Your Molded Parts
Your injection molded parts can be refined through various processes to improve their function and appearance. Methods include surface coatings, electroplating, metallizing, printing, and laser engraving. These techniques offer protection, decorative effects, and the possibility of customizing the parts.
At FACTUREE, your laborious search for different suppliers comes to an end. We take the maximum load off you and offer complete services from a single source:
- Mechanical polishing and chemical smoothing
- Various coatings, from spraying to electroplating
- Printing and patterning techniques, laser marking, and hot stamping
- Assembly and mounting
Speed is Key – Rapid Prototyping (= Rapid Injection Moulding)
Do you want to advance your innovations quickly and need prototypes flexibly and promptly? We offer rapid prototyping. This includes techniques for quickly producing a physical model or prototype of a part or product. These methods allow design ideas to be tested and improved quickly and efficiently.
This is the key to faster and more cost-effective development of components. We use efficient and economically attractive prototyping techniques to produce pre-series versions of injection-molded parts. This allows engineers and designers to quickly create physical models of components to check their shape, fit, and function before expensive tools are made for mass production.
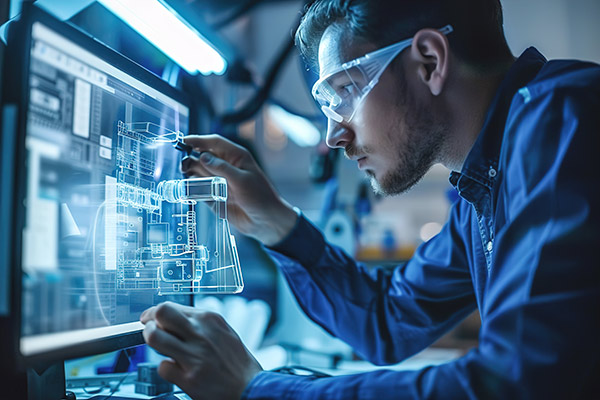
In rapid prototyping, depending on the components and required specifications, a whole range of fast production processes are used and sometimes combined, typically 3D printing, vacuum casting, rapid injection molding, and CNC. Conventional injection molding is mainly supplemented by the efficient processes of vacuum casting and rapid injection molding.
Speed
Prototypes can be produced in a shorter time compared to traditional methods by using efficient techniques.
Design Verification
Engineers and designers can receive physical models of their components early on to check the design and make any necessary changes before expensive tools are made.
Cost Savings
Since no expensive tools need to be made for mass production, the costs for prototype production are lower.
Flexibility
As rapid prototyping processes are based on digital 3D models, changes to the design can be made quickly and easily to test different design options.
And We Can Do Even More:
Other Methods for Manufacturing Metal and Plastic
In addition to injection molding, we have other processes in our portfolio, each with specific advantages for various applications – from batch size 1 to mass production:
Particularly suitable for producing highly precise components with complex shapes and thin wall thicknesses, as needed in electronics housings and automotive components. Suitable for larger quantities.
Particularly suitable for the production of highly precise components with smooth surfaces and fine details. The process is ideal for producing prototypes, small series, and decorative parts in various industries such as automotive, aerospace, and electronics.
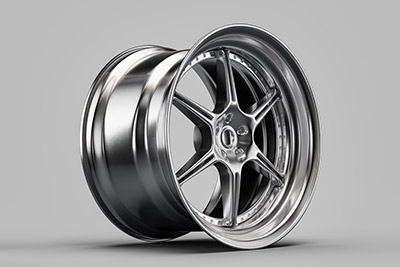
Gravity Casting
Particularly suitable for the production of components with large dimensions and a high material density. This process is often used for the production of cast parts with uniform density and low porosity, as required in the aerospace and mechanical engineering industries.