Perfection in Detail – with Our Vacuum Casting Services
Are you looking for a process to produce intricate plastic components with smooth surfaces? Then vacuum casting is the ideal choice. Whether you need complex geometries, fine surface textures, or robust prototypes, vacuum casting offers the flexibility and precision your projects demand.
With various material options and finishing possibilities, vacuum casting opens new avenues for your innovations. This process is perfect for producing prototypes, pre-production, small series, and decorative parts across various industries, including automotive, aerospace, and electronics.
At FACTUREE, you benefit from personalized consultation for your specific needs, fast production times, cost-efficiency, and the highest precision and perfect surface quality of your vacuum-cast parts.
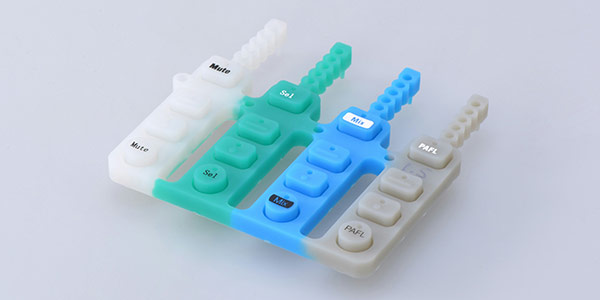
Advantages of Vacuum Casting at FACTUREE
Vacuum casting is the optimal solution for the quick, precise, and cost-effective production of high-quality plastic components. This casting process is highly adaptable, quickly implementable, and nearly free of tooling costs. We offer you:
-
Precision and Detail
Tolerances ranging from ±0.2 mm to ±4 mm, depending on customer specifications and part size -
Excellent Surface Quality
Parts exhibit a smooth, high-quality surface that usually eliminates the need for post-processing -
Rapid Prototyping
Ideal for fast production of prototypes and small series, significantly reducing development times
-
Cost Efficiency
Low tooling costs allow for quick production of cast parts -
Diverse Material Options
Efficient processing of a wide range of materials -
Reduced Production Times
Leading to faster product market introduction -
Scalability
Suitable for small production runs -
Customization and Flexibility
A variety of requirements can be met – tailored solutions -
Everything from a single source
Including all standard post-processing like surface finishing, engraving, etc. -
Personal Contact
Competent and personal consultation by experts
Dimensions and Tolerances
With the vacuum casting process, components in a wide variety of sizes can be produced. Small parts are just as feasible as very large components up to 2 × 1 × 1 meters.
While vacuum casting is not as precise as plastic injection molding, it still achieves small tolerances, aligned with DIN 16742-TG5 standards. The minimum tolerance is ±0.1 mm, with general tolerances around 0.4 – 0.5%. For higher dimensional accuracy, allowances and CNC post-processing should be considered. The minimum wall thickness is 0.75 mm, though a wall thickness of 1.5 mm is recommended for optimal results.
FACTUREE ensures precise manufacturing of components using vacuum casting – with a wide range of dimensions and optimal tolerances. Our advanced manufacturing methods and state-of-the-art machines in our extensive production network ensure the reliable fulfillment of your specific requirements for form, size, and precision.
Material Options for Your Vacuum-Cast Parts
Our material options provide a variety of mechanical, thermal, and chemical properties to meet the needs of various applications. The choice of material depends on the end product requirements, such as strength, flexibility, heat resistance, and chemical resistance.
Your personal contact is available to help you find the right material for your project.
- ABS-like
- ABS-like, UL94-V0 (flame retardant)
- ABS-like, heat resistant up to 120°C or up to 200°C
- ABS-like, glass-filled
- ABS-like, antistati
- PMMA (Acrylic)-like, transparent
- PMMA (Acrylic)-like
- POM-like
- PP/PE-like
- PC-like
- PA-like
- Rubber/TPU/TPE-like
- PA-like
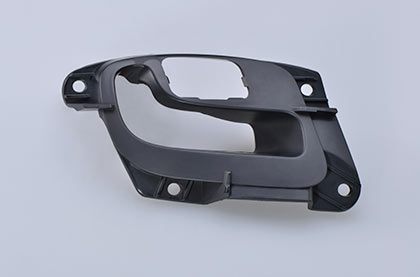
Color pigments can be added to the casting resins for a variety of color options. Different materials can be combined in one component, enabling the production of multi-component parts such as hard-soft connections.
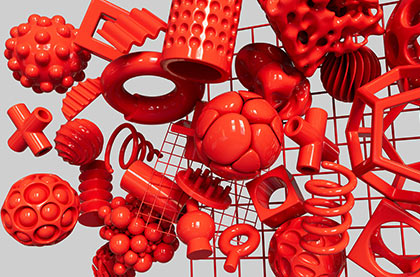
Vacuum casting is suitable for high-quality surfaces, comparable to the very good surface quality of injection-molded parts.
The extensive search for different suppliers ends with us. We offer comprehensive services from a single source, relieving you to the maximum. Your vacuum-cast parts can be refined through various processes to enhance their function and appearance:
- Varnishing
- Coating
- Gilding and Silvering
- Laser Engraving
- Hot Stamping
- Polishing
- Assembly and mounting
- Thread Insert Installation, etc.
- Post-Processing of Allowances (e.g., for tighter tolerances)
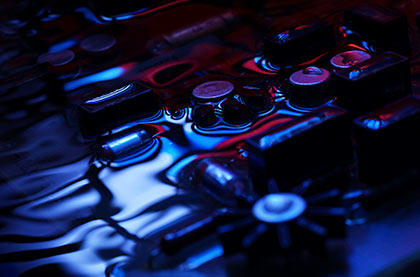
Speed is Key – Rapid Prototyping (= Rapid Injection Moulding)
Do you want to advance your innovations quickly and need prototypes flexibly and promptly? We offer rapid prototyping. This includes techniques for quickly producing a physical model or prototype of a part or product. These methods allow design ideas to be tested and improved quickly and efficiently.
This is the key to faster and more cost-effective development of components. We use efficient and economically attractive prototyping techniques to produce pre-series versions of injection-molded parts. This allows engineers and designers to quickly create physical models of components to check their shape, fit, and function before expensive tools are made for mass production.
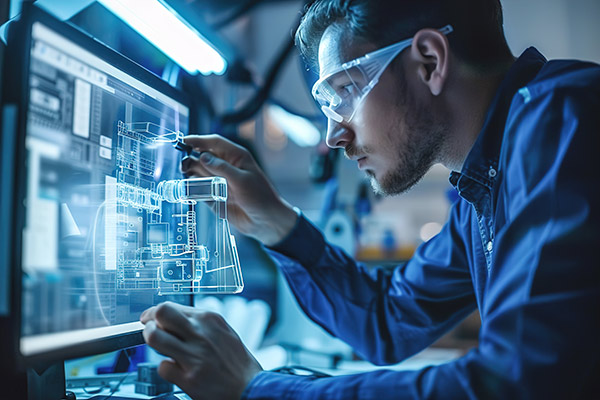
In rapid prototyping, depending on the components and required specifications, a whole range of fast production processes are used and sometimes combined, typically 3D printing, vacuum casting, rapid injection molding, and CNC. Conventional injection molding is mainly supplemented by the efficient processes of vacuum casting and rapid injection molding.
Speed
Prototypes can be produced in a shorter time compared to traditional methods by using efficient techniques.
Design Verification
Engineers and designers can receive physical models of their components early on to check the design and make any necessary changes before expensive tools are made.
Cost Savings
Since no expensive tools need to be made for mass production, the costs for prototype production are lower.
Flexibility
As rapid prototyping processes are based on digital 3D models, changes to the design can be made quickly and easily to test different design options.
And We offer more: Additional Processes
for Metal and Plastic Parts Manufacturing
In addition to injection molding, we have other processes in our portfolio, each with specific advantages for various applications – from batch size 1 to mass production:
Ideal for mass production. Suitable for complex parts with precise details and tight tolerances. Proven for various applications in industries such as automotive, electronics, medical technology, packaging, and consumer goods.
Particularly suitable for producing highly precise components with complex shapes and thin wall thicknesses, as needed in electronics housings and automotive components. Suitable for larger quantities.
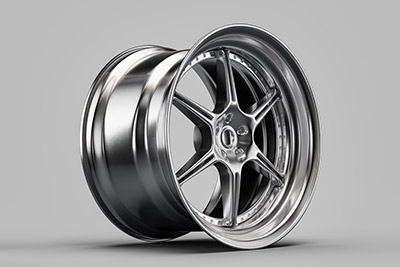
Gravity Casting
Particularly suitable for the production of components with large dimensions and a high material density. This process is often used for the production of cast parts with uniform density and low porosity, as required in the aerospace and mechanical engineering industries.